What is a JSA? Understanding Job Safety Analysis for Safer Workplaces
Grace Clueit 6 min readDiscover what a Job Safety Analysis (JSA) is and how it can enhance workplace safety. Learn more about its importance for a safer work environment.
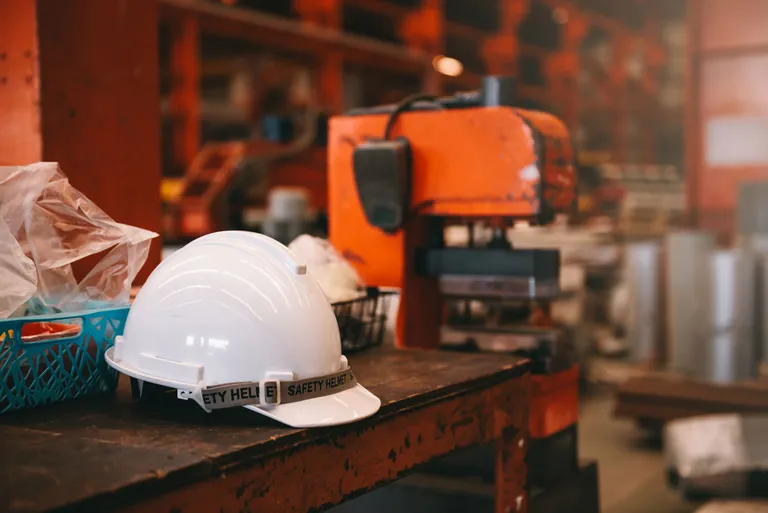
Job Safety Analysis (JSA) Meaning Explained
First of all, what is a JSA? This guide aims to help you understand, create and evolve your Job Safety Analysis risk assessment and provide your workforce with a smooth, clear, structured and safe experience.
What is a JSA?
A Job Safety Analysis, JSA, is a risk assessment process that provides guidance on identifying hazards and risks involved with a task or job, risk control measures and steps on how it should be carried out safely in your workplace.
It is an important WHS regulation that helps companies establish and break down what could go wrong, how to avoid it, and ultimately keep their workers safe within necessary job procedures.
What is a JSA used for?
A Job Safety Analysis can be used for any task or job (as opposed to only high-risk construction work in a safe work method statement). It can be applied across various industries with a physical element, such as construction, mining, utilities and logistics.
Here are some practical applications of a JSA in the workplace:
You have a new contractor who is not familiar with working at heights and the risk of a person falling
Your workers are required to do an unfamiliar task in a different and higher-risk environment than normal
You have a specific work assignment on a new piece of equipment or machinery
A dangerous near-miss has occurred recently on the same task in your workplace
Asbestos work is being carried out, and personal protective equipment is required to ensure workers are protected
When is a JSA required?
A Job Safety Analysis is not a legal obligation. Still, it is a safe practice for activities that may pose a risk. Here are some examples of when a JSA may be required:
- Jobs that are different to the normal requirements of a workplace or workers
- If there are hazards that may put the workers at risk
- If there are new workers who are not familiar with the task or process
- An error, hazard or near-miss has previously occurred during this type of task
- If new hazards that have not been dealt with before are present
Key Components of a JSA
Here are the 7 key critical components of a Job Safety Analysis, JSA:
- Identify the job or task
- Outline the steps involved
- Establish potential hazards
- List control measures using Hierarchy of Controls
- Fill out JSA form
- Communicate with your workforce
- Monitor, update and evolve your JSA document and process
Understanding the JSA process: Step-by-step breakdown
Here’s a step-by-step breakdown of how to conduct a JSA using 7 key critical components:
1. Identify the job or task
Identify the job or task at hand. JSAs are only required if your team’s job or task is out of the ordinary - e.g., when a task/person is new or unfamiliar.
2. Outline the steps involved
Clearly outline the steps for each task in order of how they’re performed. No need to go too micro here; a helicopter overview of each step is ideal.
3. Identifying hazards
Identify potential hazards involved with the task. List your job hazard breakdown clearly in plain English, no matter how small some potential risks may seem. Identifying potential hazards such as asbestos work, risk of falling objects or other workplace hazards is an important step within risk evaluations.
4. List control measures
Ensure the correct risk control measures are listed for the task so that your workforce knows how to avoid hazards on a job. For example, a safety control measure within your JSA process might indicate that workers need to wear personal protective equipment (PPE) during a job.
5. Fill out JSA form - following a JSA template, you’ll need to include the following:
- Department
- Location/site/address
- Supervisor
- Individual/team
- Creation date
- Revision date
- Job/task
- Potential hazards
- How to avoid/control measures
- Training required for task
For more information, head to our guide on JSA templates here.
6. Get on the same page with your workforce
Ensure you communicate the JSA with your workforce; everyone is on the same page and fully understands the job/task/hazards.
7. Monitor, update and evolve JSA
Keep on top of things and ensure the JSA is followed and adhered to. If any mistakes or near-misses occur, ensure you update the JSA to factor this in and avoid the same mistakes in future.
How to implement a JSA effectively in an organisation
Here’s how to effectively enforce JSAs into your day-to-day operations:
Start at the top:
Ensure all leadership and management are trained and prepared to conduct and oversee JSAs.
Staff training and input:
Ensure your staff are trained on JSAs, when to use them, and how to identify hazards and control measures. Real-life scenarios are a great way to teach your staff about when and where they may apply. Get frontline workers involved too - they are the ones on the ground and may have better or practical examples of when JSAs may be needed in your industry.
Creation, storage and access:
Don’t overcomplicate the process. Make your JSAs simple and user-friendly to encourage proper use. Create templates and store them in an easy-to-access and centralised folder. Digital format is highly recommended to save workers from having to print/scan JSAs - we want to make it as straightforward as possible.
Common challenges in conducting a JSA
Here are some of the typical challenges that professionals face while conducting JSAs:
- Lack of time or rushed completion - Sometimes, a JSA may be rushed or incomplete due to time pressures, leading to mistakes, missing information and misunderstandings.
- Improper hazard identification - Hazards may accidentally be missed or misidentified within a JSA.
- Unsatisfactory control measures - Control measures listed on the JSA may not be adequate.
- Lack of clarity with workers - Workers may agree and sign without understanding the task or hazard.
JSA vs other safety documents: SWMS, JHA
To help you further understand a Job Safety Analysis, here’s a comparison table among other key safety documents.
Document: | Features | Main differences |
---|---|---|
Job Safety Analysis JSA | Tasks broken down into steps. Potential safety hazards were identified for each task, and appropriate control measures were provided. | Not legally required but recommended. Can be focused on any day-to-day task that poses a hazard, rather than high-risk construction work. |
Safe Work Method Statement SWMS | Safe work method statements show how to perform HRCW safely and include responsibilities, safety measures and review formats. | Legally required in every state and territory. For HRCW (high-risk construction work) activities. |
Job Hazard Analysis JHA | Same as a JSA, tasks broken down and risks/hazards identified. | Referred to as JHA (Job Hazard Analysis) rather than JSA by some states or industries. |
Final thoughts: Enhancing safety with a JSA
JSAs are an integral part of health and safety and safe work procedures, and it is so important for safety-conscious organisations to conduct them. From reduced accidents, improved safety culture, increased task clarity and more empowered employees, there are so many long-term benefits of implementing a Job Safety Analysis that will enhance your safety operations and reduce risks.
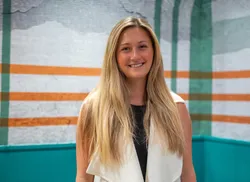
Grace Clueit
Marketing Manager
This article was written by Grace Clueit, Altora’s Marketing Manager. Grace has significant experience in marketing and writing.
This content was 100% human-created.